AMS 2750G is in force! Pyrometry standard AMS 2750 has been updated again.
- Utku Inan
- Jul 14, 2022
- 7 min read
The temperature measurement standard AMS 2750, one of the important standards for the heat treatment world, was recently renewed when we least expected it. Version F was repealed as of June 30, 2022, after remaining in force for 2 years.

As I said before on my Linkedin account, I prepared this review by reading during the holiday. I hope that will be useful.
AMS 2750G First impressions:
First, let's take a look at the historical evolution of AMS 2750. As can be seen in the table below, the F version, which we have been using for two years, was the least used after the A version published in 1987.
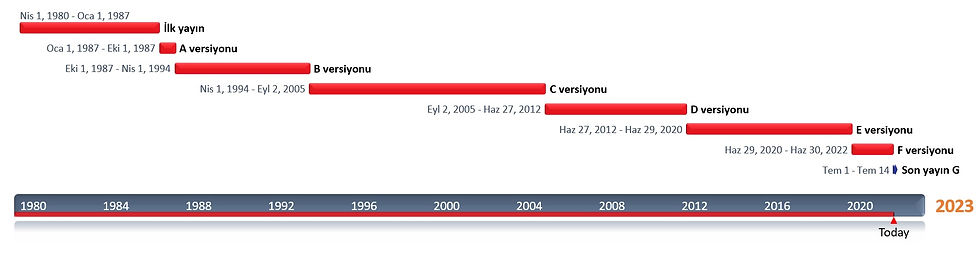
Another thing that caught my attention is that there is a significant increase in the price of the standard. While I bought the old versions for $87, the price requested for this new version AMS 2750G is $134 . This corresponds to a price increase of 54%.
Since this update is not a rewrite, you will see an ( l ) sign on the left next to the changed sections. There are 79 changes in total.
Let's make a little reminder, if the AMS document is completely rewritten, there will be an ( R ) symbol in parentheses in the title. If you remember, AMS 2750F was like this.
After giving one more detail within the scope of unnecessary information, I will move on to the review. While the old version was 54 pages, AMS 2750G is 56 pages.
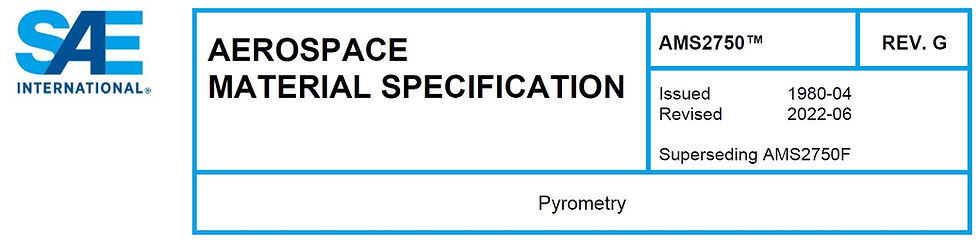
The investigation begins,
I will not evaluate all 79 amendment articles here, but I will try to consider them as main sections in general. I tried to italicize the renewed topics so that they can be distinguished more easily. I think it will be easier if you pay attention to this.
An additional change has come to the reference documents:
AS7766 Terms Used in Aerospace Metals Specifications has been replaced with ARP 1917 Clarification of Terms Used in Aerospace Metals Specifications used in the F version.
A new standard that was not in the old one has been added to the references. You can obtain this standard for Temperature Electromotive Force (emf) Tables for Unlettered Thermocouple Combinations from the ASTM website for $98.
Definitions:
A total of 20 changes. This number is about a quarter of the total changes. I have listed below what I found worth paying attention to.
The M type example in the definition of base metal thermocouple has been removed.
I can say that the definition of digital instrumentation (device) has been expanded. Since most oven users in our country use new equipment, it is not very effective.
The phrase "these devices are mostly portable" in the field test device description has been removed.
Clearer terms have been added to the calibration frequency table.
RTDs have been added to the definition of noble metal sensors (thermocouples).
A definition has been added for sensors whose thermoelements consist mainly of refractory metals (e.g. Tungsten, Rhenium, Tantalum, Niobium and Molybdenum) and their alloys.
The definition of sensitivity has been completely removed.
Table reference numbers in SAT definitions have changed. The definitions are written with slightly clearer meanings.
Changes to technical requirements,
Temperature Sensors
While there was no detail about attaching a thermocouple to the part in the old standard, such a statement has now been added.
Spot welding of thermoelements directly to a part, simulated part, or heat sink is permitted for temperatures ≤2000 °F or 1100 °C.
While the calibration intervals and calibration accuracies remain the same in the sensors and sensor calibration table ( Table 1 ), the previously written temperature tolerances for type B sensors have been removed.
Table 2 explains more clearly that K type extension cables and connectors can be used in the connections of M type thermocouples.
In Table 3 we have a new row. If the measuring tip of your MIMS thermocouple is exposed to the oven environment, you should consider this thermocouple as "expendable".
A type C thermocouple, which was not there before, has been added to the TUS&SAT sensors section in Table 5 .
Article 3.1.7 "Refractory" has been added to "Reuse of SAT and TUS Sensor".
Article 3.1.10 regarding charging thermocouples is generally the same, but a type C thermocouple has been added and some clearer sentences have been added.
The temperatures used for Table 6 are the same, but they have become clearer numerically.
Instrumentation
Here we encountered a new requirement,
3.2.1.4 Process recording data collection shall be a minimum of six data points for each recorded sensor during each time at temperature processing cycle not to exceed 10-minute intervals.
3.2.1.5 Data collection intervals shall be sufficient to demonstrate conformance to cooling rate requirements.
3.2.1.5.1 The recording instrument shall actively record/collect data during the entire time that parts or raw material are in the thermal processing equipment. In cases where load sensors must be disconnected to transfer the load, users shall have other objective evidence of process compliance (e.g., data showing temperature drop from the temperature of other furnace recording sensor(s) compliant with the soak period).
There is only one change in Table 7, and that is the replacement of the term Zener voltage with the term "precision voltage reference".
Test instruments (device) were collected under a single title. (Primary Standard, Secondary Standard and Field Tester)
Devices used at a single temperature can be calibrated at a single temperature.
3.2.3.1 All control, recording and overtemperature devices will be digital. The 0.1 °C screen sensitivity rule has been extended for another year .
Some information that should be included in the device calibration report has been updated.
There is no change in the requirements regarding Correction and Change offsets in Article 3.2.6.1 , but the sentence meanings have been clarified.
SAT ( System Accuracy Test)
The article explaining which sensors are required for SAT has been made a little clearer.
The SAT shall be performed on all control and recording systems required by the applicable instrumentation type,
as well as any additional recording systems used for parts and raw material acceptance in each control zone of each piece of thermal processing equipment used for production heat treatments.
Another example has been added to the examples given for when SAT is needed. This is an example that explains why SAT is required if you are using a sensor from a different roll.
Although the alternative SAT requirements are generally the same, it has been added to the standard that alternative SAT can be used for A, C or D+ instrumentation if the control and recording sensor life span is shorter than the SAT interval.
TUS
We can say that there is no big change in the TUS section of the standard. The relevant TUS tables remain the same. The requested homogeneities are the same, the TUS intervals are the same.
The paragraph regarding TUS sensor locations has been made a little clearer and I am sharing the text below. You can also see below a few items whose application is originally the same but whose description has been changed in the standard.
3.5.1.4 During initial and periodic TUS, the dimensions of the measurement connection locations of corner sensors for a square or rectangular work zone or perimeter sensors for a cylindrical work zone shall define the ends of the work zone such that no heat-treated material extends beyond them.
3.5.8.6 For vacuum furnaces operated at partial pressure (with filling gas) during production, at least one of the periodic TUSs must be performed annually at at least one operating temperature and within the partial pressure range used in production. The gas used will be one of the gases used during production.
3.5.13.1 TUS sensor or recording channel failure is not permitted in corner locations of a rectangular/square workspace or perimeter (top/bottom or front/back) positions of a cylindrical workspace. A temporary condition such as a short or loose connection where normal temperature indication is restored will not be considered a faulty TUS sensor.
Relocation of Hot or Cold Recording Sensors for Type A and C Instrumentation
This subject is essentially the same in practice, only two drawings have been added to the standard for a clearer understanding. I cannot share the drawing due to copyright reasons, but I will try to explain.
If the homogeneity in the oven is better than half of the requested range, we do not replace the hot and cold recording sensors.
Example,
If the expectation from the oven is ±8°C and the TUS result remains within ±4°C, do not make any changes.
In a different example, if the difference between the old "cold" point and the new "cold" point as a result of the TUS is less than the maximum allowed SAT difference, we do not make any changes. Of course, this also applies to the hot sensor.
Example,
The maximum SAT difference allowed in your oven is ±2.2°C or ±0.4% of the temperature reading (as a reminder, you can see these values in Tables 11 and 12). As a result of your TUS, the new hot spot is 1.5°C different from the old hot spot. Then you do not have to change the location of this sensor.
Radiation Research
You will see a revision bar in this article. The requirements are the same, but there is an addition regarding aluminum brazing furnaces.
3.5.17.5 For aluminum vacuum brazing equipment using clamping fixtures, panels should be placed in the fixture to repeat production.
3.5.17.5.1 The number, aluminum alloy and size of panels can be adjusted to increase production.
Evaluation and Conclusion:
If you look at the details I tried to explain above, the AMS 2750G revision did not bring any dramatic changes. It would be a realistic comment to say that the definitions and sentences have become clearer in general. Since I know that pyrometry is the branch with the most non-compliance written in all aviation heat treatment inspections, an AMS 2750 version using such clearer expressions will provide convenience for users.
Comments