Failure analysis in sheet metal forming die
- Utku Inan
- Jun 8, 2020
- 2 min read
We investigated the cause of damage to the molds due to the formation of cracks after heat treatment in mold parts made of X100CrMoV5 (1.2363) cold work tool steel material.

A total of 4 parts were heat treated together and during the last inspection, it was noticed that two of them were damaged. Despite the strong finding noticed in the first stage of the damage analysis (visual control), other possibilities were reviewed one by one before reaching the final decision. I will tell you these steps below.
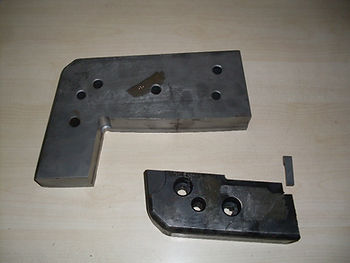
First of all, the possibility of an error in the heat treatment procedure was evaluated. Bakery records were examined.
Preheating temperatures were consistent with routine heat treatment temperatures.
The austenitizing temperature and time were in accordance with the recipe specified by the manufacturer for the material.
Tempering temperatures were as they should be.
The desired hardness was 54-56 HRC and the found value was 54.5 HRC.
A sample was removed from one of the damaged parts for microstructural and chemical analysis. The chemical analysis result did not deviate from the values specified in the material's standard. No inclusions, alloy banding, or dangerous carbon networks were observed in the material. The carburization or decarburization effect that may occur from the material surface to the inside during heat treatment was reviewed. There was no problem.
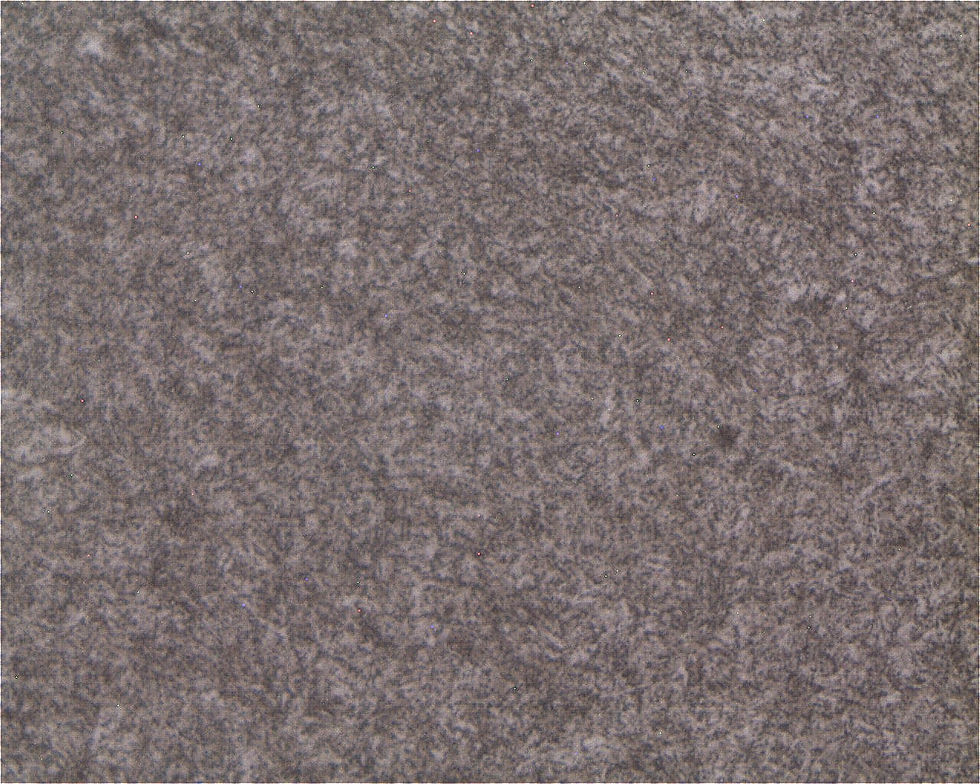
The heat treatment microstructure was smooth at 500x magnification. In light of these results, we returned to the initial finding.
Now I have to share with you the first finding of the damage analysis,

Two of the four parts that were heat treated together had a dense burr residue at the crack initiation site. The edges of the other two pieces were deburred.
These fine burrs first heat up faster than the body during heating, and then cool down faster than the body during cooling. This heating-cooling difference causes stresses on the material, and in such cases, the crack formed in the burr can propagate into the body of the material.
Many mold, tool or part manufacturers do not care about the burrs that cause this damage, and even emphasize this by saying that it is not important, we will clean it after the heat treatment when warned.
To summarize, burrs left on the material surface, inside and around the holes, sharp corners without chamfers, transitions without fillets and large cross-section differences are at risk. No matter how careful the heat processor is, these risks must be eliminated before heat treatment.
Comments