Magnesium alloys and heat treatments
- Utku Inan
- Jun 27, 2020
- 4 min read
Magnesium, which is of great importance for our health, is also of serious importance for engineering applications as the lightest structural metal , and it seems that it will have an even stronger place with developing manufacturing and heat treatment methods.
In this article, I will examine the magnesium alloys and their heat treatments used in a camera body, car rims, an engine block or helicopter transmission box, and even football boots.

Magnesium often forms alloys with aluminum, zinc, manganese, silicon, copper and zirconium. Metal can be shaped by methods such as injection, extrusion, forging and sand casting.

Magnesium alloys have good specific strength and easy machinability in applications that do not provide high temperature resistance.
They are examined in three groups,
1. Magnesium-Manganese alloys:
They have good weldability and can be manufactured as thin plates. Example, MgMn2 or MgMn1.5 alloys
2. Magnesium-Aluminium-Zinc alloys:
They are produced by metal injection, sand casting, extrusion and forging, and can gain strength with heat treatment. Example, AZ81A or AZ63A
3. Magnesium-Zinc-Zirconium and Thorium alloys:
They have good impact toughness, machinability and corrosion resistance. Their strength increases with heat treatment. Example, ZK61A, AZ31A or HZ11
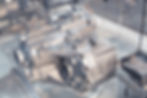
There is no common standard for naming magnesium alloys as there is for steel or aluminum materials. They are often referred to by the initials of the alloys they contain, as defined in ASTM B275 .
For example, AZ91C gets its name from the 9% aluminum and 1% zinc it contains. The letter C comes from the fact that it is recorded as the 3rd alloy similar to this composition. Depending on the heat treatment status of the material, the following letter and a number are added to the end.
F: As fabricated
O: Annealed
H1 : Cold formed
T4: Taken into solution
T5: Artificially aged
T6: Solution taken and aged
The full name of the alloy is: AZ91C-T6
Heat treatments of magnesium alloys:
Magnesium alloys can be heated in air in applications up to 450°C . However, at higher temperatures, a protective environment should be used. Oxidation that may occur on the surface of magnesium alloys will greatly reduce the strength values. Additionally, the protective atmosphere prevents the risk of magnesium burning at high temperatures ( over 600°C ). Inert gases can be used, as well as carbon dioxide, sulfur hetafluoride and sulfur dioxide gases. They must be absolutely free of processing oils, dirt and dust before being loaded into the furnace. They are not suitable for heat treatment in salt baths. Ovens where the processes will take place ±6 It must operate with °C precision.
The parts are subjected to full annealing in order to relieve the stresses that may occur after the forming operations. Process temperature is between 290 - 455°C .
Stress relief is applied to reduce stresses in all rolled, cold drawn, welded, forged, machining and cast magnesium alloys. Cast parts, in particular, require stress relieving as they are susceptible to stress corrosion. Stress relief temperatures are between 260 - 425°C, depending on the alloy .
Unlike other metals, they have very long solution times. Section thickness and alloy type are the biggest factors that change this period. For example, while ZK61A is put into solution at 493 - 502 °C for 2 hours, AM100A with the same thickness is kept at 421 - 432 °C for 16-24 hours. While almost all of them can be cooled with air or pressurized gas, some exceptional alloys require water cooling.
EQ21A3, EV31A3 and QE22A3 alloys should be cooled in a water bath at 60-91 °C.
Some magnesium alloys, like aluminum alloys, are aged at low temperature for a long time or at relatively high temperature for a short time. Some must be aged at a single temperature.
For AZ92A alloy T5, it must remain at 232 °C for 5 hours or 260 °C for 4 hours. The T6 heat treatment of the same alloy is at 218 °C for 5 hours or at 168 °C for 16 hours.
In order for ZK61A alloy to reach T6 quality, it must remain at 129 °C for 48 hours.
Effects of heat treatment on magnesium alloys
Hardness control can be made in magnesium alloys after heat treatment. However, hardness measurement alone cannot symbolize mechanical properties. Brinel and Rockwell E method is used.
The most effective method to determine the aging level is tensile testing and microstructure analysis. Magnesium alloys show different etching properties for different temper temperatures.
For example, when the ZE41A alloy is etched in the cast structure, it etches blue, while when T5 is heat treated, it etches to a brownish tone.
The mechanical properties of ZK61A (UNS M16611) , whose heat treatment temperatures I have given above, after T6 aging are as follows;
Tensile strength: 310 MPa
Yield strength: 195 MPa
Hardness: 80 HV
For detailed mechanical properties of this alloy, you can review the link below,
Thanks to their high specific strength, they can withstand certain temperatures ( 90 - 100°C ). Their use in engineering applications is increasing in parallel with the developments in manufacturing methods and heat treatments.
In this article, I tried to summarize the magnesium alloys and their heat treatments, which are already used today but I think will take more part in our lives in the coming days. I hope it was useful.